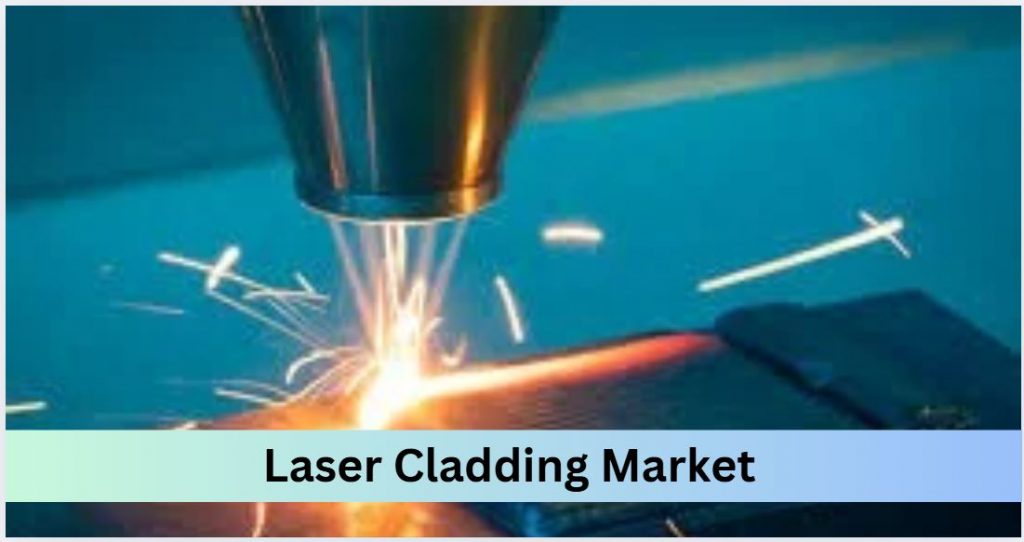
Market Overview
The Global Laser Cladding Market is projected to grow from USD 612.62 million in 2024 to USD 1,262.51 million by 2032, at a compound annual growth rate (CAGR) of 9.46%. This robust expansion is fueled by the increasing demand for high-performance, wear-resistant surfaces across key industries such as aerospace, automotive, oil & gas, and energy. The growing emphasis on equipment reliability and operational efficiency has led industries to adopt surface enhancement techniques that extend the service life of components. In sectors where equipment replacement costs are high, laser cladding provides an economical alternative. Additionally, growing concerns over downtime and repair costs are pushing manufacturers to explore preventive maintenance technologies like laser cladding. This trend is especially prevalent in energy and heavy machinery industries that rely on robust component protection.
Laser cladding, a surface modification technique, utilizes a high-powered laser to deposit a coating material onto a substrate, enhancing properties like hardness, corrosion resistance, and durability. As industries seek to extend the lifecycle of high-cost components while minimizing downtime, the relevance of laser cladding has intensified globally. This process significantly reduces material waste, offers metallurgical bonding, and provides a high degree of precision—making it more efficient than conventional welding or thermal spraying techniques. Furthermore, the precision of laser cladding helps in achieving uniform coating thickness, essential for critical applications. It also enables multi-material deposition, expanding its usability in complex systems. Manufacturers are increasingly integrating laser cladding with CNC systems for better automation. These integrations are proving particularly valuable in high-throughput industrial settings where time and quality are paramount.
In the current global context, the drive for industrial efficiency and sustainability aligns with the advantages of laser cladding. The technology is particularly valuable in repair applications, enabling significant cost savings and extending the usable life of components. Additionally, the adoption of automation and Industry 4.0 practices supports the integration of laser cladding into modern manufacturing systems. Governments and industries worldwide are investing in advanced manufacturing technologies, further boosting the demand for laser cladding solutions. With innovations in fiber lasers and alloy materials, the market is witnessing a steady technological evolution that opens new avenues for application across various verticals. As more sectors move toward predictive maintenance models, laser cladding is expected to play a central role. Key market players are focusing on R&D to enhance material compatibility and process scalability. Collaborative efforts between academia and industry are accelerating innovation in cladding technology. All these factors collectively suggest a promising and resilient future for the laser cladding industry.
Download Sample Report: https://www.credenceresearch.com/report/laser-cladding-market
Market Drivers
Increased Demand for High-Performance Materials
Industries such as aerospace and oil & gas operate under extreme conditions where wear, corrosion, and temperature resistance are critical. Laser cladding enhances the surface properties of components, improving performance and longevity. This demand for durable, reliable equipment is a major growth driver. Heavy machinery, turbines, and transmission systems often face severe operational stress, requiring superior surface integrity. Laser cladding ensures these parts can endure longer intervals between servicing. Moreover, in aerospace, cladding is increasingly used to upgrade existing materials without the need for complete replacement. This not only reduces maintenance costs but also enhances safety standards. The trend toward lightweight yet strong materials in critical sectors adds to the growing utility of cladding technologies.
Advancements in Laser Technology
Technological improvements in laser sources—especially fiber and diode lasers—have increased process efficiency and cost-effectiveness. Modern lasers offer higher beam quality, stability, and energy efficiency, enabling precise material deposition. These advancements make laser cladding more accessible and scalable across industries. The emergence of compact laser systems has enabled mobile and on-site repair capabilities. These systems are particularly useful in aerospace and marine environments where equipment is too large to transport. Innovations like beam shaping and closed-loop process control also contribute to superior surface finish. Continuous improvements are enabling cladding of newer material types including titanium and Inconel alloys. These upgrades are making laser cladding suitable for a broader range of high-tech applications.
Emphasis on Cost Reduction and Sustainability
Organizations are under growing pressure to reduce costs and minimize environmental impact. Laser cladding reduces raw material consumption and waste by targeting only worn-out or exposed areas. It also enables component repair over replacement, cutting costs and supporting circular economy practices. Compared to traditional coating techniques, laser cladding uses significantly fewer resources while achieving better performance metrics. Its precision reduces the need for post-processing and rework, saving both energy and material. Laser cladding also helps industries comply with environmental regulations by limiting emissions and resource waste. By extending component life, it indirectly reduces the demand for mining and material extraction. These sustainability benefits are increasingly critical in modern industrial strategies.
Adoption of Industry 4.0 and Smart Manufacturing
The integration of robotics, AI, and IoT in manufacturing systems complements the use of laser cladding. Automation allows for consistent quality, repeatability, and scalability. Smart factories are increasingly incorporating laser cladding systems into their production lines to stay competitive and innovative. Real-time monitoring and adaptive control systems ensure optimal performance during the cladding process. Cloud-based data analytics can now track the wear behavior of components, triggering maintenance alerts before failures occur. These advancements enable more accurate forecasting of equipment maintenance needs. Integration with ERP and MES systems ensures better coordination across the supply chain. As a result, laser cladding becomes a strategic tool in end-to-end smart manufacturing ecosystems.
Market Challenges
High Initial Investment
Implementing laser cladding requires substantial capital expenditure for equipment and facility setup. Small and medium enterprises (SMEs) may find it financially challenging to adopt this technology, especially in emerging economies with limited funding options. The cost of maintenance and skilled labor also adds to the overall financial burden. Return on investment may be delayed in low-volume production scenarios. Furthermore, industries unfamiliar with laser processes may hesitate to make the leap without guaranteed results. Although long-term savings are considerable, the up-front commitment deters many potential adopters. Overcoming this barrier often requires government subsidies or collaborative research initiatives.
Complex Process Parameters
The laser cladding process involves numerous parameters such as laser power, scan speed, and powder feed rate. Ensuring the right combination of these variables requires expertise and precision. Improper calibration can lead to poor adhesion, cracks, or unwanted residual stresses. Advanced simulation tools are necessary to predict outcomes and avoid costly errors. Environmental conditions like humidity and temperature can also affect cladding quality. The need for specialized pre- and post-treatment processes further complicates implementation. Consequently, companies must invest in rigorous training and high-fidelity testing environments. Inadequate process control can lead to suboptimal results, reducing the potential benefits of the technology.
Skilled Workforce Shortage
Operating and maintaining laser cladding equipment demands specialized technical knowledge in lasers, metallurgy, and automation. The global shortage of such skilled professionals restricts market expansion, particularly in regions where industrial training infrastructure is underdeveloped. This shortage is exacerbated by the rapid pace of technological change, requiring continual upskilling. Many technicians lack experience in integrating laser systems with robotics and control software. Companies often need to invest heavily in training or outsourcing, which can increase operational costs. Collaborative programs between universities and industries are slowly filling the talent gap. However, widespread availability of skilled professionals remains a work in progress.
Regulatory Compliance and Quality Assurance
Industries like aerospace and medical devices require strict adherence to quality and safety standards. Laser cladding systems must meet rigorous certifications, making market entry complex for new players. Ensuring uniformity and defect-free surfaces across batches remains a challenge. Audits and inspections often involve costly downtime and resource allocation. In some regions, regulatory bodies may lack clear guidelines for laser-based technologies, creating ambiguity. Manufacturers must also invest in advanced non-destructive testing (NDT) tools to verify component integrity. Failure to meet these standards can result in disqualification from high-value contracts. Consequently, the regulatory burden adds another layer of complexity to market participation.
Market Opportunity
Expansion in Aerospace & Defense Applications
The aerospace industry is exploring laser cladding for turbine blade repair, landing gear hardfacing, and other high-value components. The ability to restore expensive parts without compromising integrity presents a significant cost-saving opportunity, especially for military and commercial fleets. With increasing air travel and defense budgets, the demand for component restoration has grown sharply. Laser cladding offers lightweight and high-strength coatings essential for aircraft systems. The method’s precision ensures minimal thermal distortion, which is crucial for aerospace tolerances. Additionally, partnerships between OEMs and MRO providers are fostering innovation in this area. These developments signal a bright future for cladding in aviation applications.
Rise in Renewable Energy Investments
Wind turbines and solar energy infrastructure demand components with extended operational lifespans. Laser cladding enables the protection of gearboxes, shafts, and fasteners from harsh environmental exposure, supporting the long-term efficiency of renewable energy systems. With global energy policies emphasizing green transitions, durability of equipment becomes paramount. Cladding reduces maintenance frequency in offshore wind farms where access is limited. The technique is also being used for protecting hydraulic systems and energy converters. Enhanced corrosion resistance through laser cladding extends mean time between failures (MTBF). This reliability can significantly improve the ROI of renewable energy projects.
Emerging Markets in Asia Pacific and Latin America
Countries like India, Brazil, and Mexico are investing in modernizing their manufacturing and defense sectors. As these regions scale industrial operations, demand for cost-effective repair and surface treatment solutions such as laser cladding is on the rise. Infrastructure development and foreign direct investments (FDIs) are key enablers. Domestic manufacturing programs are incorporating laser cladding into new production lines. These economies benefit from a large labor pool and increasing access to global technologies. Regional trade agreements are also facilitating equipment importation and technical collaboration. Government incentives for industrial modernization further support market entry and expansion.
Material Innovation for Specialized Use Cases
Advancements in alloy formulations and carbide blends are opening new frontiers for laser cladding applications. These materials enhance performance under specific operating conditions, allowing for customized solutions in mining, automotive, and marine industries. Material R&D is focusing on improving adhesion strength, thermal conductivity, and fatigue resistance. Nano-composite coatings are also gaining attention for their superior characteristics. These innovations are enabling more targeted applications with higher efficiency. Specialized coatings are now being developed for bio-compatible and food-grade environments. Overall, material science advancements are pushing the boundaries of what laser cladding can achieve.
Market Segmentation
Based on Type:
- Fiber Laser
- Diode Laser
- CO₂ Laser
- Acoustic Laser
- Others
Based on Materials:
- Cobalt-based Alloys
- Nickel-based Alloys
- Iron-based Alloys
- Carbides & Carbide Blends
Based on End-use:
- Aerospace & Defense
- Automotive
- Mining
- Oil & Gas
- Energy & Power
- Others
By Region
North America
- U.S.
- Canada
- Mexico
Europe
- Germany
- France
- U.K.
- Italy
- Spain
- Rest of Europe
Asia-Pacific
- China
- Japan
- India
- South Korea
- Southeast Asia
- Rest of Asia-Pacific
Latin America
- Brazil
- Argentina
- Rest of Latin America
Middle East & Africa
- GCC Countries
- South Africa
- Rest of the Middle East and Africa
Regional Analysis
North America
North America leads the laser cladding market due to strong demand from aerospace and oil & gas sectors. The U.S. is at the forefront, with substantial investments in repair technologies and defense applications. Canada and Mexico contribute through automotive and mining industries. The presence of leading OEMs and technology developers also strengthens the region’s market share. Additionally, the growing focus on predictive maintenance in U.S. manufacturing boosts adoption. Government defense contracts and funding for military-grade refurbishment further drive laser cladding use. Universities and research institutions in the region play a pivotal role in advancing laser technologies. The U.S. also benefits from a skilled workforce and early adoption of Industry 4.0 frameworks.
Europe
Europe holds a significant market share, driven by Germany, the U.K., and France. These countries have a high concentration of automotive and energy companies actively using laser cladding. Regulatory support and innovation in materials science also strengthen market performance. The European Union’s push for sustainable industrial processes aligns well with the material efficiency offered by laser cladding. Furthermore, investments in rail and renewable infrastructure create additional demand for durable surface coatings. Germany, in particular, is home to several laser equipment manufacturers and R&D hubs. The presence of robust industrial automation capabilities in Western Europe enhances integration of laser cladding systems into existing lines. Ongoing collaboration between public and private sectors sustains innovation in this space.
Asia Pacific
Asia Pacific is witnessing the fastest growth, with China, India, and Japan spearheading the adoption of laser cladding. Investments in infrastructure, aerospace, and smart factories are rising. Rapid industrialization and government-backed technology upgrades fuel regional momentum. China leads with its expansive manufacturing base and increasing focus on high-precision component restoration. India is investing in defense and public infrastructure projects, creating opportunities for protective surface coatings. Japan’s advanced robotics industry is enabling automated laser cladding solutions. Growing demand from shipbuilding and railway sectors also supports regional adoption. Additionally, government incentives for advanced manufacturing and local production of laser systems are further catalyzing market growth.
Latin America
Latin America, especially Brazil and Argentina, is emerging as a growing market. The focus on mining and oil exploration creates demand for protective coating solutions. Though adoption is still nascent, opportunities are expanding with foreign investment. Industrial modernization initiatives in the region are incorporating laser-based technologies. Brazil’s mining and metallurgy sectors present key application areas for wear-resistant coatings. Collaborations with North American and European firms are accelerating technology transfer. Regional academic institutions are also beginning to explore applied research in laser surface engineering. As awareness grows, laser cladding is gaining ground in high-value machinery maintenance applications.
Middle East & Africa
This region is leveraging laser cladding to support energy and defense initiatives. The GCC nations are investing in manufacturing diversification, while South Africa is using laser cladding for mining equipment maintenance. Technological partnerships play a key role here. UAE and Saudi Arabia are actively pursuing smart industrialization as part of their national transformation plans. Demand for durable and corrosion-resistant coatings in petrochemical facilities is also growing. South Africa’s mining industry is seeing steady adoption of laser cladding for restoring costly mechanical parts. Emerging laser labs and vocational training centers are helping build local technical expertise. Import substitution strategies are encouraging regional players to invest in domestic laser repair capabilities.
Top Companies
- LaserBond Limited
- TLM Laser Ltd
- Lumibird
- Lincoln Laser Solutions
- Kondex Corporation
- LaserStar Technologies Corporation
- Hoganas AB
- Hayden Corporation
- Lumentum Operations LLC
- RUMPF Group
Future Outlook
- The laser cladding market will continue to benefit from rising demand in the aerospace sector. Enhanced durability and repair capabilities will reduce lifecycle costs of critical components.
- Integration with robotics and smart manufacturing systems will streamline operations. This will make laser cladding viable for mass production and highly precise applications.
- Ongoing improvements in fiber laser technology will reduce energy consumption and enhance beam control. This will lead to lower operational costs and increased adoption.
- Innovations in alloy powders and composite blends will expand usage in extreme environments. Industry-specific formulations will drive specialized application growth.
- Sustainability trends will favor laser cladding for its ability to extend equipment life. Reduced material waste and repair-focused strategies will support eco-friendly practices.
- The renewable sector will increasingly use laser cladding to protect infrastructure. Components in wind and hydro power systems will benefit from extended wear resistance.
- Integration with AI will enable real-time process control and fault prediction. These technologies will improve product quality and process reliability.
- Countries in Asia and Africa will adopt laser cladding as part of industrial modernization. Local demand will increase with new investments in manufacturing.
- Public-private partnerships and academic collaborations will accelerate innovation. Focused R&D will lead to next-gen cladding technologies.
- Simulation and digital twin tools will enhance design accuracy and quality assurance. Faster prototyping will support broader use across industries.
Download Sample Report: https://www.credenceresearch.com/report/laser-cladding-market