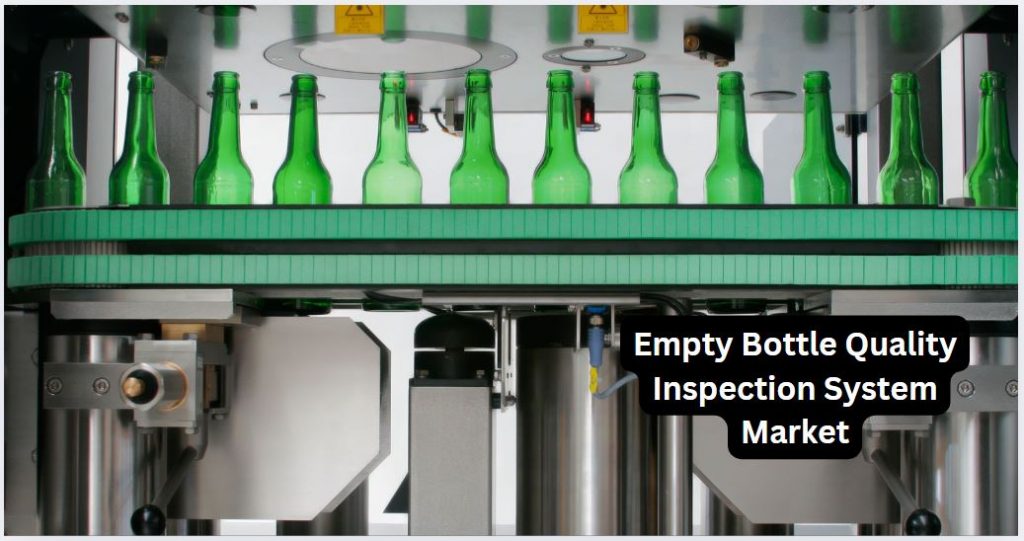
Market Overview
The Empty Bottle Quality Inspection System Market size was valued at USD 1700 million in 2024 and is anticipated to reach USD 2492.6 million by 2032, growing at a CAGR of 4.9% during the forecast period (2024-2032). This significant growth highlights the crucial role of quality inspection systems in ensuring product safety and compliance across industries like food and beverage, pharmaceuticals, and personal care. In a global environment increasingly focused on quality assurance, waste reduction, and automation, these systems are becoming indispensable.
Empty bottle inspection systems provide critical support by detecting defects, contaminants, and other quality issues before the bottling process, minimizing product recalls and production downtime. With the rise in consumer expectations for product safety and brand reliability, manufacturers are investing heavily in advanced inspection technologies. Additionally, strict regulatory frameworks regarding hygiene, labeling, and packaging quality have amplified the need for reliable inspection mechanisms.
The market’s relevance is further emphasized by the global shift toward Industry 4.0 practices. Companies are adopting machine vision, AI-based inspection, and IoT-enabled systems to improve efficiency and traceability. As industries move towards smarter manufacturing practices, the empty bottle quality inspection system market is poised to experience consistent growth. This market’s evolution directly correlates with the increasing complexity of supply chains, the need for reduced waste, and the heightened focus on sustainability and operational excellence.
Download Sample Report: https://www.credenceresearch.com/report/empty-bottle-quality-inspection-system-market
Market Drivers
Growing Demand for Automated Quality Control
The push toward automation across industries is a major driver for the empty bottle inspection system market. Manufacturers seek efficient, reliable, and repeatable solutions to minimize human errors and enhance throughput. Automated systems enable real-time defect detection, faster decision-making, and seamless data recording, making them vital for industries aiming for consistent quality. As companies increasingly integrate smart factory solutions, demand for automated inspection systems will continue its upward trend. In addition, rising labor costs globally are motivating manufacturers to substitute manual inspections with automated solutions. The scalability and adaptability of automated systems make them an attractive long-term investment. Thus, the growing pursuit of operational excellence is significantly boosting the market.
Stringent Regulatory Standards for Product Safety
Rising enforcement of product safety regulations worldwide is significantly influencing market growth. Regulatory bodies like the FDA, EU regulators, and others impose strict guidelines on manufacturing processes, especially for consumable goods. Companies must ensure defect-free packaging to meet quality standards and avoid penalties or recalls. Consequently, manufacturers are investing in advanced inspection systems to meet these compliance requirements, driving market adoption. The focus on achieving international certifications further strengthens the importance of quality inspections. Moreover, consumer awareness regarding product safety is adding pressure on brands to ensure impeccable packaging standards. As a result, regulatory compliance continues to be a key driving force.
Increased Focus on Reducing Operational Costs
Companies are constantly seeking ways to cut operational costs without compromising quality. Empty bottle inspection systems help detect defects early in the production process, preventing wastage of materials, labor, and energy. Early detection translates to significant cost savings by reducing recalls and rework expenses. This cost-efficiency aspect is a major motivating factor for businesses to adopt sophisticated inspection solutions. Additionally, cost optimization through automation enhances competitiveness in price-sensitive markets. Businesses are also focusing on reducing downtime, which further adds value to investing in inspection systems. Hence, operational efficiency is directly influencing technology adoption in manufacturing units.
Technological Advancements in Inspection Systems
Rapid advancements in machine vision, AI algorithms, and sensor technologies are reshaping the market landscape. Modern inspection systems are capable of detecting micro-defects that were previously impossible to identify. Features like 360-degree bottle inspections, non-contact testing, and machine learning integration enhance inspection accuracy and speed. Technological innovation remains a vital pillar propelling market growth, making inspections smarter, faster, and more reliable. AI-driven predictive maintenance is also minimizing system failures and enhancing uptime. Cloud-based analytics is enabling real-time monitoring and remote diagnostics, increasing system efficiencies. As the Fourth Industrial Revolution advances, technological evolution will continue to open new horizons.
Market Challenges
High Initial Investment Costs
One of the significant challenges hindering market expansion is the high upfront investment required for installing automated inspection systems. Small and medium-sized enterprises (SMEs) may find the cost prohibitive, delaying adoption. Although long-term savings are notable, the barrier to entry remains high for many companies, especially in developing regions. Additionally, the cost of ongoing maintenance and upgrades further burdens initial buyers. Financing options and government subsidies remain limited in many countries. This financial hurdle restricts many small manufacturers from adopting high-end inspection solutions despite their long-term advantages.
Complex System Integration
Integrating inspection systems with existing production lines poses technical challenges. Differences in equipment compatibility, production speeds, and bottle shapes can complicate the deployment of inspection technologies. Companies must customize solutions to match specific operational needs, often requiring additional engineering expertise and costs, thereby slowing adoption. Integration downtime can disrupt production schedules, creating additional revenue loss. Training staff to operate new systems is another hidden cost often overlooked. In industries with high throughput, even small misalignments in system integration can cause significant losses.
Evolving Regulatory Requirements
Constant updates and variations in global regulatory standards create compliance complexities for manufacturers. Keeping inspection systems updated to meet changing regulations can be resource-intensive. Failure to maintain compliance could result in fines or production stoppages, creating operational risks for businesses relying heavily on static systems. Different regional requirements add further layers of complexity. Multinational companies often need region-specific inspection settings to meet localized standards. Staying ahead of regulatory changes demands continuous investment in compliance management.
Risk of Technological Obsolescence
The fast pace of technological evolution poses a risk of rapid obsolescence for existing inspection systems. Companies investing heavily today may find their systems outdated within a few years. This uncertainty leads to hesitancy among buyers, especially for expensive hardware solutions that require significant capital investment. The rapid introduction of AI, machine learning, and advanced sensors accelerates obsolescence cycles. Businesses must weigh the risks of investing now versus the potential costs of waiting. Lack of standardized upgrade paths further complicates long-term investment decisions.
Market Opportunity
Expansion into Emerging Economies
Rapid industrialization in emerging markets presents lucrative growth opportunities. Countries like India, Vietnam, and Brazil are witnessing increased demand for packaged goods, boosting the need for quality control systems. Manufacturers expanding into these regions can leverage first-mover advantages by offering affordable, scalable inspection solutions tailored to local needs. The expanding middle-class population and evolving consumer expectations further enhance prospects. Government initiatives promoting industrial growth provide additional incentives. Consequently, emerging economies are becoming attractive investment destinations for inspection solution providers.
Development of Compact, Modular Systems
The market is shifting towards compact and modular inspection systems that offer scalability and easy integration. These solutions appeal to small and medium-sized manufacturers who seek flexible investments. The ability to customize inspection capabilities according to changing production demands will unlock new customer segments. Modular systems reduce installation time and cost, making them accessible to a broader audience. Manufacturers favoring lean manufacturing practices also prefer modular setups. The rising demand for flexible production lines is anticipated to fuel this trend further.
Growing Demand in Non-Alcoholic Beverage Segment
The rise of health consciousness is fueling the non-alcoholic beverage market, including bottled water, juices, and energy drinks. This surge is directly translating to higher demand for empty bottle inspection systems to ensure hygiene and quality. Companies specializing in non-alcoholic beverages represent a growing customer base for inspection solution providers. Premiumization trends are increasing the emphasis on flawless packaging. Consumer loyalty increasingly depends on perceived quality, putting inspection systems at the heart of brand value protection. Hence, beverage manufacturers are prioritizing investments in inspection technologies.
Partnerships and Collaborations
Strategic alliances between inspection technology companies and manufacturing firms offer new opportunities for growth. Joint ventures help in expanding technological capabilities and reaching new markets faster. Companies collaborating on R&D projects can offer advanced, cost-effective solutions, creating a competitive edge and tapping into underserved markets. Shared resources reduce the cost burden and speed up innovation cycles. Partnered solutions offer greater reliability and broader service networks. Such collaborations are becoming essential strategies for sustaining long-term market growth.
Market Segmentation
By Component
- Hardware
- Software
By Technology
- Machine Vision
- X-ray Inspection
- Ultrasonic Inspection
By Application
- Food and Beverage
- Pharmaceuticals
- Cosmetics and Personal Care
- Household Products
By Inspection Type
- Online Inspection
- Offline Inspection
By Region
North America
- U.S.
- Canada
- Mexico
Europe
- Germany
- France
- U.K.
- Italy
- Spain
- Rest of Europe
Asia-Pacific
- China
- Japan
- India
- South Korea
- Southeast Asia
- Rest of Asia-Pacific
Latin America
- Brazil
- Argentina
- Rest of Latin America
Middle East & Africa
- GCC Countries
- South Africa
- Rest of the Middle East and Africa
Regional Analysis
North America
North America maintains a dominant position, driven by high automation adoption and stringent regulatory requirements. The U.S. leads due to heavy investments in R&D and strong presence of major market players. Canada and Mexico are also witnessing increased industrial automation, bolstering demand for inspection systems. Rising emphasis on food and pharmaceutical safety standards boosts market penetration. Additionally, innovation hubs in the U.S. drive continuous product advancements. Technological leadership and high consumer safety awareness keep the region at the forefront.
Europe
Europe remains a robust market, propelled by strict quality standards and consumer expectations for sustainable practices. Countries like Germany, the UK, and France lead adoption rates. The region’s focus on reducing production waste and enhancing operational efficiency encourages investment in modern inspection technologies. Regulatory frameworks like CE certifications mandate strict adherence to safety. Growth of eco-friendly packaging also increases inspection requirements. Europe’s commitment to Industry 4.0 transformations sustains its strong demand.
Asia Pacific
Asia Pacific is the fastest-growing market, fueled by rapid industrialization and urbanization. China, India, and Japan dominate the region with significant investments in beverage, food, and pharmaceutical sectors. Government initiatives promoting manufacturing upgrades contribute to the market’s accelerated expansion. Rising disposable income boosts demand for packaged consumer goods. Focus on quality assurance in export-oriented economies like China and Vietnam spurs adoption. The shift towards digital factories across Asia Pacific propels the inspection systems market forward.
Latin America
Latin America’s market is evolving steadily, with Brazil and Argentina at the forefront. Rising urbanization and improving economic conditions are encouraging companies to upgrade manufacturing infrastructure. However, economic volatility remains a limiting factor for broader adoption across the region. Focus on improving export capabilities drives investments in quality control. Local governments are encouraging industrial modernization through favorable policies. Despite challenges, Latin America offers promising mid-term growth opportunities for inspection solutions.
Middle East & Africa
The Middle East is showing promising growth, with the UAE and Saudi Arabia investing heavily in manufacturing modernization. Increasing demand for packaged beverages and pharmaceuticals is driving the adoption of inspection systems. Regional players focus on premium quality production to meet international standards. Initiatives like Saudi Vision 2030 aim to diversify economies, boosting industrial sectors. Africa presents emerging opportunities, particularly in Nigeria and South Africa. Growing awareness about product quality and safety, coupled with initiatives from international organizations, supports market growth. Export-focused production facilities necessitate stringent quality inspections. As a result, technology adoption rates in this region are rising consistently.
Top Companies
- Mettler-Toledo International Inc.
- Antares Vision S.p.A.
- Mekitec Group
- Krones AG
- Heuft Systemtechnik GmbH
- Brevetti C.E.A. Spa
- Teledyne TapTone
- SACMI Imola S.C.
- Filtec (Industrial Dynamics)
- Peco InspX
Future Outlook
- The global empty bottle inspection system market is poised for robust growth, fueled by increasing automation trends across industries. Companies will continue prioritizing efficient quality control, opening avenues for advanced system providers.
- Technological innovations such as AI-driven defect recognition and machine learning are expected to redefine inspection capabilities. Systems will become smarter, more accurate, and capable of predictive maintenance to avoid downtime.
- Expansion into untapped emerging markets will offer significant growth potential for manufacturers. Localized, cost-effective solutions will be key to penetrating these high-growth regions.
- The rise of smart factories and Industry 4.0 will accelerate the adoption of integrated inspection systems. Seamless data connectivity and IoT-based systems will dominate future production lines.
- Non-contact, high-speed inspection technologies will gain popularity in sectors like pharmaceuticals and food & beverage. These advancements will enhance safety, hygiene, and production throughput.
- Sustainability initiatives will push manufacturers to adopt eco-friendly production practices. Inspection systems that minimize material wastage and optimize resource use will find strong market demand.
- Customized modular systems designed for specific bottle types and industry needs will become mainstream. Flexibility and scalability will remain essential for future buyers.
- Partnerships between AI companies and inspection technology providers will drive disruptive innovations. Collaborative R&D efforts will deliver next-generation, cost-efficient inspection systems.
- Adoption of cloud-based data analytics for inspection insights will grow rapidly. Companies will leverage real-time data for quality optimization and predictive decision-making.
- As regulations tighten globally, compliance-focused inspection solutions will surge in demand. Future systems will need to adapt quickly to evolving safety and quality standards.
Download Sample Report: https://www.credenceresearch.com/report/empty-bottle-quality-inspection-system-market