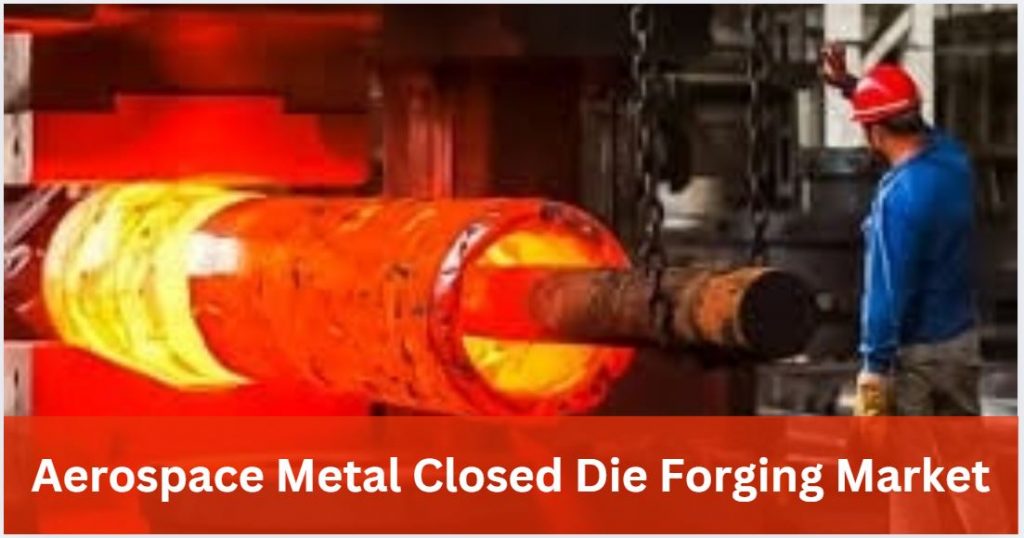
Market Overview
The Aerospace Metal Closed Die Forging Market is projected to grow from USD 83,406.5 million in 2024 to an estimated USD 142,559.59 million by 2032, with a compound annual growth rate (CAGR) of 6.93% from 2024 to 2032. The increasing demand for high-strength, lightweight, and reliable aerospace components is driving market expansion. The aerospace industry heavily relies on closed die forging for critical applications such as engine components, landing gear, and structural parts. This method ensures superior mechanical properties, making it indispensable for high-performance aircraft manufacturing.
Forged components offer exceptional durability, resistance to extreme conditions, and cost-effectiveness, making them a preferred choice for aerospace manufacturers. Additionally, advancements in material science, including the development of titanium alloys and high-strength aluminum, are enhancing the efficiency and reliability of forged parts. As global aviation demand rises, aircraft manufacturers are increasing their production rates, further propelling the closed die forging market.
The market’s significance is further reinforced by the growing focus on fuel efficiency and sustainability. Airlines and aircraft manufacturers are continuously striving to reduce fuel consumption and carbon emissions, leading to increased adoption of lightweight forged materials. The expansion of the space exploration sector, with companies like SpaceX and Blue Origin investing in new aerospace technologies, also contributes to market growth. Moreover, rising defense expenditures across key nations are boosting the demand for forged aerospace components in military aircraft.
Regionally, North America leads the market, primarily due to the strong presence of Boeing, Lockheed Martin, and key forging companies. Europe follows closely, with Airbus driving demand for forged components. Asia Pacific is emerging as a high-growth region, with China and India investing heavily in aerospace manufacturing. The expansion of low-cost carriers and defense modernization programs in these regions will further propel market growth. As the aerospace industry evolves, closed die forging will remain a critical process for ensuring the safety, performance, and efficiency of aircraft components.
Access the Full Report: https://www.credenceresearch.com/report/aerospace-metal-closed-die-forging-market
Market Drivers
Rising Demand for Lightweight and Durable Aerospace Components
Aircraft manufacturers are increasingly prioritizing weight reduction to improve fuel efficiency and reduce operational costs. Closed die forging plays a crucial role in achieving this goal by producing lightweight yet durable components for critical aircraft parts. Materials like aluminum, titanium, and nickel-based alloys are extensively used due to their high strength-to-weight ratio and corrosion resistance. These materials help aircraft meet strict weight regulations while maintaining structural integrity. The demand for lightweight aircraft is further fueled by stringent environmental regulations aimed at reducing carbon emissions. Airlines are shifting toward fuel-efficient aircraft, increasing the demand for forged landing gears, turbine components, and structural reinforcements. Additionally, electric and hybrid aircraft development is expanding the scope of closed die forging applications, as these aircraft require optimized structural components. The industry’s growing emphasis on recyclable and sustainable materials also presents new opportunities for eco-friendly forging technologies.
Growth in Commercial and Military Aviation
The global aerospace industry is witnessing rapid expansion, particularly in commercial aviation due to increasing passenger traffic. Emerging economies like China, India, and Brazil are witnessing higher air travel demand, prompting aircraft manufacturers to ramp up production. Leading companies, including Boeing and Airbus, have substantial order backlogs, indicating sustained demand for aerospace components. The military aviation sector is also driving market growth, with governments increasing their defense budgets to modernize fleets. Countries such as the United States, China, and India are investing in next-generation fighter jets, helicopters, and unmanned aerial vehicles (UAVs), all of which require forged components for enhanced durability. The emergence of hypersonic aircraft and space exploration programs is further fueling the demand for high-performance forging solutions.
Advancements in Forging Technology
The integration of advanced manufacturing technologies such as automation, AI-driven design, and precision machining has revolutionized the forging industry. These technologies enable higher production efficiency, reduced material wastage, and improved component accuracy. Modern forging techniques now incorporate real-time monitoring and predictive maintenance, reducing downtime and operational costs. 3D modeling and simulation software help optimize forging dies and press parameters, ensuring better consistency in output. The adoption of Industry 4.0 in aerospace manufacturing is also driving process innovations, leading to higher efficiency and lower production costs.
Stringent Regulations and Safety Standards
Aerospace components must adhere to strict quality and safety standards to ensure aircraft reliability. Regulatory bodies such as the Federal Aviation Administration (FAA) and European Union Aviation Safety Agency (EASA) enforce rigorous standards for aerospace materials and manufacturing processes. Closed die forging ensures compliance with these regulations by producing high-precision, defect-free components. The increasing complexity of aerospace designs and performance requirements has also heightened the demand for quality-certified forging solutions.
Market Challenges
High Initial Investment Costs
Setting up advanced closed die forging facilities requires significant capital investment. The cost of high-tonnage forging presses, precision machining tools, and skilled labor adds to the financial burden. Additionally, research and development (R&D) costs for innovative forging techniques further elevate expenses. Small and medium-sized enterprises (SMEs) face difficulty in competing with established players due to financial constraints. Despite high demand, many forging companies struggle with the long return-on-investment (ROI) period, limiting market entry for new participants.
Supply Chain Disruptions
The aerospace industry relies on a complex and interconnected supply chain for sourcing titanium, aluminum, and nickel alloys. Geopolitical tensions, trade restrictions, and raw material shortages can disrupt production. The COVID-19 pandemic highlighted vulnerabilities in global supply chains, causing delays in aircraft manufacturing. Many forging companies are now focusing on regionalized supply chains to reduce dependency on specific countries and mitigate risks.
Intense Competition from Alternative Manufacturing Processes
Additive manufacturing (3D printing) and composite materials are gaining traction as potential alternatives to traditional forging. These technologies offer design flexibility, reduced material usage, and shorter lead times, posing a challenge to the forging industry. However, while 3D printing excels in prototyping and complex geometries, it lacks the strength and durability required for critical aerospace applications. As a result, forging remains the preferred choice for structural components.
Environmental and Sustainability Concerns
The forging process involves high energy consumption and emissions, leading to concerns over carbon footprints and environmental impact. Regulatory bodies are enforcing stringent emission control measures, pushing manufacturers to adopt eco-friendly forging methods. The transition to sustainable energy sources, green manufacturing, and recyclable materials is becoming crucial for long-term growth. Companies investing in low-emission forging technologies will have a competitive edge in the future.
Market Opportunity
Rising Demand for Next-Generation Aircraft
The aerospace industry is witnessing a shift toward next-generation aircraft, driven by fuel efficiency, performance optimization, and sustainability. With increasing airline passenger traffic, aircraft manufacturers such as Boeing, Airbus, and Embraer are focusing on lightweight materials and fuel-efficient designs. The demand for high-performance forged components in modern aircraft is expected to surge as airlines seek cost-effective operations. The development of electric and hybrid aircraft also presents a lucrative opportunity for the forging industry. These aircraft require high-strength structural components that can withstand varying electrical and thermal loads. With the emergence of urban air mobility (UAM) and eVTOL aircraft, closed die forging will play a critical role in enhancing component durability and safety.
Expanding Defense and Space Programs
The global aerospace industry is witnessing an increase in defense spending and space exploration initiatives. Governments are heavily investing in fighter jets, surveillance aircraft, and UAVs, all of which demand precision-forged components for enhanced durability. Additionally, the expansion of space programs by agencies such as NASA, ESA, ISRO, and private firms like SpaceX and Blue Origin is boosting demand for high-strength forged parts. Components used in rocket engines, spacecraft structures, and satellite deployment systems must withstand extreme forces, making closed die forging the preferred manufacturing method.
Technological Innovations in Forging Processes
Advancements in automation, AI-driven design, and high-speed forging are enhancing production efficiency and reducing material waste. The adoption of computer-aided engineering (CAE) and digital twin technology allows manufacturers to optimize forging parameters in real time, ensuring higher accuracy and lower rejection rates. Furthermore, the integration of smart sensors and IoT-enabled monitoring systems helps detect defects early, reducing downtime and production costs. As manufacturers embrace Industry 4.0, the forging industry will witness higher operational efficiency and increased competitiveness.
Emerging Markets in Asia-Pacific and the Middle East
Developing regions such as Asia-Pacific and the Middle East are expanding their aerospace manufacturing capabilities. Countries like India and China are investing in domestic aircraft production, creating new opportunities for local forging companies. Additionally, the rise of low-cost carriers and increasing air travel demand in these regions is boosting aircraft production, further driving the demand for closed die forging solutions. Governments are also providing subsidies and incentives to encourage local manufacturing, fostering market expansion.
Market Segmentation
Based on Product:
- Press Capacity Below 10,000 MT
- Press Capacity Between 10,000 and 19,000 MT
- Press Capacity Between 20,000–29,000 MT
Based on Application:
- Engine Components
- Landing Gear and Structural Components
- Helicopter Rotor Components and Shafts
By Region:
North America
- U.S.
- Canada
- Mexico
Europe
- Germany
- France
- U.K.
- Italy
- Spain
- Rest of Europe
Asia-Pacific
- China
- Japan
- India
- South Korea
- Southeast Asia
- Rest of Asia-Pacific
Latin America
- Brazil
- Argentina
- Rest of Latin America
Middle East & Africa
- GCC Countries
- South Africa
- Rest of the Middle East and Africa
Regional Analysis
North America
North America dominates the Aerospace Metal Closed Die Forging Market, driven by the presence of leading aerospace manufacturers such as Boeing, Lockheed Martin, and Northrop Grumman. The region boasts advanced manufacturing infrastructure and a well-established defense and commercial aviation sector. The U.S. government’s increased defense spending is further fueling the demand for forged components in military aircraft. Additionally, companies are investing in R&D to improve forging techniques and enhance material performance, ensuring high-precision and lightweight aerospace parts.
Europe
Europe is a major hub for aircraft manufacturing, led by Airbus and Rolls-Royce. The demand for lightweight, fuel-efficient aircraft is driving the need for high-strength forged components. Government initiatives promoting green aviation and carbon reduction strategies are also boosting the adoption of advanced forged materials. Countries such as Germany, France, and the U.K. are at the forefront of aerospace innovation, ensuring steady market growth.
Asia-Pacific
Asia-Pacific is one of the fastest-growing regions in the aerospace forging market. Countries like China, India, and Japan are heavily investing in domestic aircraft production and defense modernization. China’s COMAC C919 program and India’s indigenous fighter jet projects are fueling demand for locally forged aerospace components. With the region’s rising air travel demand, the market is poised for substantial growth.
Middle East & Africa
The Middle East and Africa region is witnessing growing investments in military and commercial aviation. Countries like Saudi Arabia and the UAE are focusing on expanding their aerospace manufacturing sector. The region’s strong military procurement programs are increasing demand for precision-forged aerospace parts, ensuring steady market expansion. Additionally, collaborations with global aerospace giants are strengthening the regional market presence.
Top Companies
- Arconic (United States)
- ATI (Canada)
- Bharat Forge (India)
- ELLWOOD Group Inc. (United States)
- Jiangyin Hengrun Heavy Industries Co., Ltd. (China)
- Precision Castparts Corp. (United States)
- Larsen & Toubro Limited (India)
- Scot Forge Company (United States)
- Pacific Forge Incorporated (United States)
- Somers Forge (United Kingdom)
Future Outlook
- The global aerospace industry will continue to expand, driving sustained demand for forged components.
- Increasing adoption of lightweight alloys will enhance the performance and efficiency of aerospace components.
- Advancements in automated forging and digital simulation technologies will improve precision and reduce production costs.
- The defense sector’s growing investments in next-generation fighter jets will create a steady demand for high-strength forged parts.
- Expansion of low-cost carriers and increased aircraft production will fuel market growth in emerging economies.
- Governments will continue implementing stringent quality regulations, emphasizing the need for high-precision forged materials.
- The rise of urban air mobility (UAM) and electric aircraft will expand forging applications into new aerospace segments.
- Investments in eco-friendly forging technologies will help manufacturers meet sustainability goals.
- Mergers, acquisitions, and strategic partnerships will drive market consolidation and technological advancements.
- The continued development of hypersonic and space exploration programs will further enhance market expansion opportunities.
Access the Full Report: https://www.credenceresearch.com/report/aerospace-metal-closed-die-forging-market