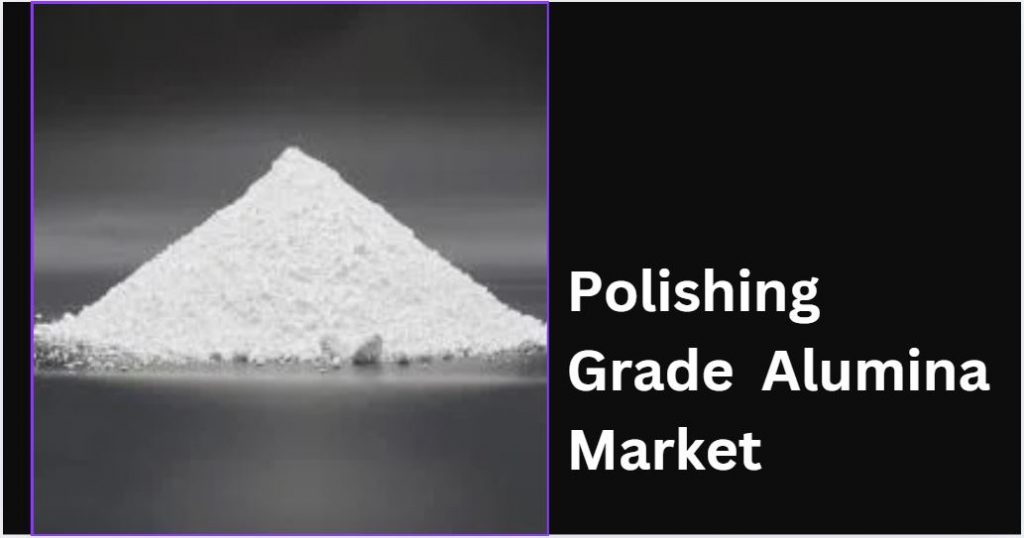
Market Overview
The Polishing Grade Alumina Market is projected to grow from USD 3,689.7 million in 2024 to an estimated USD 5,628.27 million by 2032, with a compound annual growth rate (CAGR) of 5.42% from 2024 to 2032. This upward trajectory highlights the growing demand for advanced polishing solutions across sectors like electronics, automotive, aerospace, and metal fabrication. With high hardness, chemical stability, and thermal resistance, polishing grade alumina has become a preferred material for achieving smooth surface finishes.
The relevance of this market has become increasingly pronounced due to the global shift toward high-performance and miniaturized components. Precision polishing is critical in modern manufacturing processes, especially in electronics where surface integrity directly impacts performance and durability. Similarly, the automotive and aerospace industries rely on alumina-based polishing compounds for critical components where microscopic imperfections can compromise safety or efficiency.
Additionally, the rise in global industrial production and the growing adoption of eco-friendly abrasive technologies are further propelling market demand. Environmental awareness is encouraging manufacturers to opt for polishing solutions with minimal ecological footprints, which alumina readily fulfills. As various industries push for better performance and aesthetics, the need for superior polishing materials continues to grow, ensuring a stable and promising future for the polishing grade alumina market.
Download Sample Report: https://www.credenceresearch.com/report/polishing-grade-alumina-market
Market Drivers
Boom in Consumer Electronics
Consumer electronics are becoming more compact, efficient, and feature-rich, necessitating flawless component surfaces. Devices such as smartphones, tablets, and laptops incorporate finely polished components that rely heavily on polishing grade alumina for achieving the required surface finish. As consumer demand continues to surge, so does the need for effective polishing materials. Manufacturers are increasingly focusing on miniaturized components that demand tighter tolerances and smoother surfaces. Polishing grade alumina ensures consistency in mass production, supporting lean manufacturing goals. The integration of biometric sensors and camera modules in devices further heightens the need for fine surface finishing. As wearables and smart home devices proliferate, the scope for alumina-based polishing solutions broadens. Continuous innovation in electronics will sustain long-term demand for high-performance abrasives.
Growing Automotive Manufacturing
The automotive sector, particularly electric vehicle (EV) production, is witnessing exponential growth. These vehicles require precisely polished parts to enhance efficiency, performance, and aesthetics. Polishing grade alumina provides the necessary finish quality and durability for parts like rotors, casings, and trim components, making it a vital part of automotive supply chains. Increasing emphasis on lightweight materials and aerodynamics in EVs underscores the need for precise surface finishes. Additionally, polished components contribute to energy efficiency by minimizing friction. As autonomous vehicle technologies advance, sensor housing and camera systems demand enhanced finishing. Tier-1 automotive suppliers are actively incorporating polishing processes using alumina abrasives. This sustained automotive innovation cycle directly supports alumina demand.
Advanced Industrial Applications
Industries involved in precision engineering and tooling increasingly adopt alumina-based abrasives. From turbine blades to delicate optical lenses, the need for a controlled and clean surface finish is critical. Polishing grade alumina supports high-speed polishing applications and ensures minimal surface deformation, helping manufacturers maintain stringent quality standards. Aerospace and semiconductor industries, in particular, rely on micron-level surface smoothness. Alumina’s hardness and thermal stability make it ideal for use in harsh industrial environments. Its adaptability to both wet and dry polishing systems enhances its application range. Manufacturers in sectors like watchmaking and medical devices also prefer alumina for its consistent results. With the rise of Industry 4.0, demand for precision surface finishing continues to grow.
Shift Toward Eco-Friendly Materials
Environmental concerns are shaping procurement decisions across industries. Companies are favoring materials that offer high performance with minimal environmental impact. Polishing grade alumina, being recyclable and non-toxic, aligns with global sustainability goals. This shift enhances its appeal among end users looking to minimize their carbon footprint while maintaining operational efficiency. Regulatory bodies increasingly emphasize eco-labeling and green procurement policies. Alumina’s inert nature and minimal disposal impact make it preferable to synthetic or hazardous alternatives. Industries with stringent environmental certifications now opt for sustainable abrasive solutions. Recycling alumina also reduces operational costs and aligns with circular economy principles. As green manufacturing gains momentum, alumina’s eco-profile strengthens its market position.
Market Challenges
Volatility in Raw Material Costs
Fluctuations in the cost of bauxite and energy required for alumina production can significantly impact market stability. This unpredictability makes long-term pricing strategies difficult for manufacturers, increasing the financial risk and deterring some potential investors from entering the market. Price-sensitive markets, especially in Asia and Africa, are more vulnerable to these changes. Energy price volatility, especially in Europe, adds further cost burden. Many producers are now looking into long-term contracts and hedging strategies to manage risks. Supply chain disruptions, like those witnessed during the pandemic, have exposed vulnerabilities in global sourcing. Consistent pricing remains a challenge, especially for SMEs.
High Initial Investment
Setting up manufacturing units capable of producing polishing grade alumina requires considerable capital expenditure. Advanced technologies, skilled labor, and stringent quality controls all add to the initial investment. Smaller companies often find it challenging to compete with established players due to these financial barriers. High-end production also demands automation and precision equipment. Compliance with ISO and other quality standards further escalates costs. Moreover, geographic diversification for new entrants can be cost-prohibitive. R&D investments to differentiate product grades further elevate the capital required. These financial burdens limit innovation among small manufacturers.
Strict Environmental Compliance
Although alumina is more environmentally friendly than other abrasives, its production process is still energy-intensive. Regulatory frameworks demanding emission reductions and energy efficiency add compliance pressure, often requiring process optimization or investment in clean technologies. Producers must meet local and international norms such as REACH and RoHS. Failure to comply can lead to heavy fines or production shutdowns. There is rising scrutiny over water usage and waste disposal in alumina refining. Governments worldwide are pushing for carbon neutrality, adding urgency to the compliance timeline. For older facilities, retrofitting becomes both a technical and financial challenge.
Rising Competition from Substitutes
The availability of alternative materials like silicon carbide or synthetic diamond abrasives can hinder alumina’s market share. These materials offer competitive advantages in certain applications, prompting industries to explore and sometimes switch to alternatives based on cost or performance parameters. Silicon carbide offers faster cut rates in hard materials. Synthetic diamonds are preferred for ultra-precision applications. Pricing strategies of competitors can disrupt market equilibrium. Some industries are influenced by legacy use and are slow to transition back to alumina. To stay relevant, alumina producers must emphasize cost-performance balance.
Market Opportunity
Growth in Precision Optics
The rise in demand for high-performance optical components in defense, medical, and consumer sectors presents a lucrative opportunity. Polishing grade alumina delivers the required finish for lenses, mirrors, and precision optics used in various devices, offering manufacturers a compelling value proposition. From endoscopes to camera lenses, surface clarity is paramount. Alumina’s fine particle distribution ensures uniform polishing without micro-scratches. Military-grade optics also demand rugged and defect-free surfaces. With the surge in virtual reality and augmented reality devices, new applications are emerging. This segment is expected to be a high-margin opportunity for suppliers.
Increased Focus on 3D Printing
3D printed parts often require post-processing, including polishing to ensure smooth and functional surfaces. Alumina-based polishing compounds are gaining traction as preferred post-processing solutions in additive manufacturing, particularly in metals and ceramics, opening a new segment for market expansion. The growing use of 3D printing in aerospace, healthcare, and prototyping accelerates this need. Surface finish affects both aesthetics and mechanical performance in printed parts. Alumina offers compatibility with various geometries and composite materials. As binder jetting and metal powder technologies evolve, polishing needs become more sophisticated. The role of alumina here is poised to grow rapidly.
Rise of Electric and Hybrid Aircraft
The aerospace industry’s shift toward electrification creates demand for lightweight and finely polished parts. Polishing grade alumina is poised to benefit from this trend, as more manufacturers integrate electric propulsion systems that rely on finely finished high-performance components. Aircraft interiors and engine systems need lightweight and polished surfaces for efficiency. Alumina’s heat resistance adds to its suitability for aerospace applications. With stricter fuel-efficiency regulations, aircraft parts require enhanced aerodynamic design. Global investment in urban air mobility further increases this demand. This trend offers long-term strategic growth for alumina suppliers.
Localization of Production in Emerging Markets
Countries in Asia Pacific, Latin America, and Africa are rapidly industrializing, prompting investments in local manufacturing. This creates an opportunity for polishing grade alumina producers to tap into emerging economies by establishing localized supply chains, reducing lead times, and aligning with regional demand. Governments are offering incentives to boost domestic production. Local sourcing of raw materials helps manage cost fluctuations. Customized grades for regional industries can enhance market penetration. Developing nations are becoming hubs for contract manufacturing, especially in electronics. Establishing a local footprint can ensure first-mover advantage.
Market Segmentation
By Type Segment:
- Very Soft Type
- Soft Type
- Medium Type
- Hard Type
By Application Segment:
- Metal Polishing
- Paint Polishing
- Brake Pads
- Alumina Slurry
- Others
By Region
North America
- U.S.
- Canada
- Mexico
Europe
- Germany
- France
- U.K.
- Italy
- Spain
- Rest of Europe
Asia Pacific
- China
- Japan
- India
- South Korea
- Southeast Asia
- Rest of Asia Pacific
Latin America
- Brazil
- Argentina
- Rest of Latin America
Middle East & Africa
- GCC Countries
- South Africa
- Rest of the Middle East and Africa
Regional Analysis
North America
North America remains a leading market due to its advanced manufacturing infrastructure and high demand from the aerospace and semiconductor sectors. The U.S. drives regional growth with heavy investment in R&D and advanced polishing technologies. Canada and Mexico contribute through increasing industrial output and export activities. Key players in the U.S. emphasize automation in polishing operations, boosting efficiency. There is a strong emphasis on precision finishing in defense contracts. Semiconductor fabrication facilities rely on alumina for wafer polishing. The U.S. also promotes reshoring, which may benefit domestic alumina producers. Sustainability initiatives encourage adoption of eco-friendly abrasives.
Europe
Europe shows robust growth, particularly in Germany, France, and the U.K., driven by automotive and high-tech industries. Germany’s engineering and machinery sectors demand precise components, while France and Italy show rising demand in luxury automotive and optics. Environmental regulations here also encourage cleaner polishing solutions. EU green mandates influence purchasing decisions in industrial sectors. Aerospace manufacturing hubs in Spain and the UK bolster demand. European OEMs emphasize lifecycle sustainability, favoring recyclable abrasives. Export-oriented economies support stable demand for alumina. Innovation in optical technologies in Switzerland and the Netherlands further drives niche applications.
Asia Pacific
Asia Pacific is the fastest-growing region, led by China, Japan, and India. China is a major consumer and producer of polishing grade alumina due to its large electronics and automotive base. Japan’s focus on high-precision optics and India’s expanding manufacturing ecosystem also boost regional consumption. Rapid urbanization and infrastructure growth increase material demands. Government policies support domestic manufacturing under initiatives like “Make in India.” Local availability of bauxite benefits cost competitiveness. Demand from Taiwan and South Korea’s semiconductor sectors is significant. The region’s cost advantages attract global outsourcing contracts.
Latin America
Brazil and Argentina are showing increased activity in automotive and metal processing industries. Although relatively smaller, the region presents untapped potential. Growing infrastructure and industrial investments are expected to enhance market penetration of alumina-based polishing solutions in the coming years. Trade partnerships and export corridors are strengthening supply chains. Rising disposable incomes drive domestic consumer electronics demand. Government initiatives support industrial modernization in Brazil. Mining industry collaboration offers potential for raw material integration. As local industries adopt automation, demand for precision abrasives increases.
Middle East & Africa
GCC countries are investing in high-tech manufacturing and aerospace maintenance services. South Africa contributes through its mining and metallurgy sectors. Though currently a niche market, the region shows potential as new industrial zones and free trade areas are developed. UAE and Saudi Arabia are pushing to diversify beyond oil, fostering industrial hubs. Aerospace component refurbishment demands high-quality polishing solutions. Investments in solar technology manufacturing open niche markets. The availability of natural resources can aid vertical integration. Regional demand may rise with increased participation in global supply chains.
Top Companies
- Almatis
- AluChem
- Alteo
- Sumitomo Chemical
- Hindalco
- Nabaltec
- Sasol
- Huber Advanced Materials
- Zibo Honghe Chemical Co., Ltd.
- KC Corporation
Future Outlook
- The increasing adoption of electric vehicles will continue to drive demand for finely polished components using polishing grade alumina.
- The semiconductor industry’s need for ultra-flat surfaces will boost alumina slurry consumption across production units.
- Integration of robotics in polishing operations is expected to enhance material efficiency and market productivity.
- Growth in the defense sector will fuel the demand for precision-polished optics and components.
- Customization of alumina abrasives for niche applications will provide manufacturers with competitive differentiation.
- Global efforts toward decarbonization will encourage industries to shift to alumina over synthetic abrasives.
- Investments in R&D will result in advanced alumina grades optimized for performance and sustainability.
- Asia Pacific will remain the dominant regional market due to cost-effective manufacturing and rising domestic demand.
- Supply chain integration and local sourcing will improve market resilience against raw material volatility.
- Digitalization and smart manufacturing techniques will revolutionize the production and use of polishing materials.
Download Sample Report: https://www.credenceresearch.com/report/polishing-grade-alumina-market