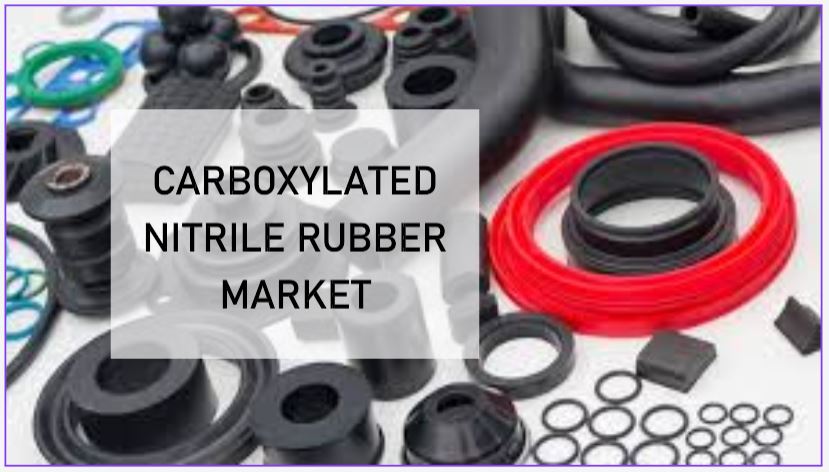
Market Overview
The Carboxylated Nitrile Rubber (XNBR) Market is set to grow significantly, expanding from USD 4,012 million in 2024 to USD 5,705.46 million by 2032, at a CAGR of 4.5% during the forecast period. This growth is primarily driven by the increasing demand for XNBR in industrial, automotive, and oil & gas applications due to its superior mechanical properties, including oil resistance, abrasion resistance, and enhanced elasticity. Industries that require high-performance rubber materials are integrating XNBR into various components to improve efficiency and durability.
The automotive industry is among the largest consumers of XNBR, using it extensively in seals, gaskets, hoses, and belts. With the rising production of electric vehicles (EVs) and advancements in fuel efficiency, the demand for high-performance elastomers is surging. Additionally, the oil & gas industry relies heavily on XNBR for its superior resistance to harsh chemicals and extreme temperatures, making it an essential component in drilling and sealing applications.
Industrial manufacturing and consumer goods sectors are also contributing to the market expansion, with increasing use in printing rolls, industrial gloves, and footwear. The footwear industry, in particular, has seen a growing preference for XNBR due to its ability to provide durable and slip-resistant soles. Furthermore, advancements in polymer technology have resulted in the development of specialized grades of XNBR, enhancing its properties and making it more versatile for diverse applications.
In addition, the market is witnessing increasing investments in research and development aimed at improving product quality, sustainability, and eco-friendly production methods. With stricter environmental regulations coming into play, manufacturers are exploring bio-based alternatives and recyclable rubber compounds to align with global sustainability goals. The market is expected to continue its upward trajectory, supported by rising industrialization, technological innovations, and expanding applications across multiple industries.
Check out the full study: https://www.credenceresearch.com/report/carboxylated-nitrile-rubber-market
Market Drivers
Growing Demand from the Automotive Industry
The automotive sector is a key driver of the XNBR market, with rising demand for durable and heat-resistant elastomers. The increasing adoption of electric vehicles (EVs) has created new opportunities for high-performance rubber materials that can withstand higher voltage systems and complex drivetrain designs. Traditional fuel-based vehicles are also incorporating advanced sealing technologies that require enhanced oil and fuel resistance, further boosting demand for XNBR.
The need for fuel efficiency and sustainability is also influencing automakers to use lightweight and durable materials in vehicle components. The use of XNBR in engine seals, belts, and vibration-dampening parts is increasing as manufacturers aim to reduce vehicle weight while maintaining performance and longevity. Additionally, governments worldwide are pushing for stricter emission regulations, requiring high-performance elastomers that can enhance engine efficiency and reduce wear and tear.
Expansion of the Oil & Gas Industry
The oil & gas sector heavily relies on XNBR for seals, gaskets, and drilling equipment due to its ability to withstand extreme temperatures and aggressive chemicals. The rising number of exploration and drilling activities worldwide, particularly in North America and the Middle East, has led to higher consumption of XNBR-based components.
Oil & gas companies are continuously seeking cost-effective and high-durability materials that can enhance operational efficiency. XNBR’s resistance to hydrocarbon fluids makes it the preferred choice for pipeline seals, downhole tools, and industrial hoses. With new oil field discoveries and expanding energy demands, the market for oil-resistant elastomers like XNBR is poised for steady growth.
Advancements in Polymer Technology
Technological innovations have led to the development of specialized XNBR grades, offering improved tensile strength, enhanced elasticity, and greater resistance to harsh environments. Advances in nano-reinforced rubber compounds and modified polymer structures are pushing the boundaries of XNBR’s performance capabilities.
With increasing research into sustainable elastomer solutions, many manufacturers are focusing on reducing processing emissions and improving recyclability. The introduction of high-performance rubber blends that combine XNBR with other elastomers is also expanding its application range across various industries, including consumer goods, aerospace, and healthcare.
Rising Adoption in Consumer Goods and Industrial Equipment
Beyond industrial applications, XNBR is gaining traction in consumer products such as footwear, gloves, and sporting goods. Its abrasion resistance, chemical stability, and flexibility make it an ideal material for high-impact applications. In the printing industry, XNBR-based roller covers and belts are becoming more popular due to their ability to withstand continuous mechanical stress.
In industrial equipment, XNBR is being used for manufacturing components that require high durability and resistance to oils, fuels, and extreme temperatures. With increasing urbanization and infrastructural development, the demand for XNBR-based products in construction, engineering, and heavy machinery is steadily rising.
Market Challenges
Volatility in Raw Material Prices
One of the significant challenges facing the Carboxylated Nitrile Rubber (XNBR) market is the fluctuation in raw material prices, particularly acrylonitrile and butadiene. Since these materials are derived from petrochemicals, their pricing is highly dependent on global oil prices, supply chain disruptions, and geopolitical tensions. Any sudden changes in crude oil prices have a direct impact on the cost of raw materials, making it difficult for manufacturers to maintain stable pricing and profit margins. Additionally, the increasing demand for petrochemical derivatives in other industries such as plastics, automotive, and construction further intensifies supply constraints, driving up costs. As a result, XNBR manufacturers are forced to adopt cost-cutting measures, alternative sourcing strategies, and inventory adjustments to mitigate price risks.
Apart from oil price volatility, the market is also affected by trade policies, tariffs, and environmental regulations imposed by governments. Restrictions on the import and export of petrochemical products can disrupt the availability of essential raw materials, causing production delays. Companies operating in regions with high dependence on imported chemicals often face the challenge of increased operational costs due to tariffs and logistical bottlenecks. This necessitates the exploration of sustainable and alternative feedstocks, but their development and commercialization require significant investments in research and infrastructure.
Environmental Regulations and Sustainability Concerns
With increasing global awareness of environmental sustainability, governments and regulatory bodies have implemented strict policies regarding the manufacturing and disposal of synthetic rubber products. The production of XNBR involves chemical processing methods that contribute to carbon emissions, hazardous waste, and water pollution. To comply with evolving environmental regulations, manufacturers must invest in greener production technologies, waste management solutions, and sustainable supply chain practices. However, these transitions often lead to higher operational costs and longer production cycles, posing a challenge to small and medium-sized enterprises (SMEs) with limited financial resources.
In addition, end-of-life disposal of synthetic rubber products remains a critical issue. Unlike natural rubber, XNBR is non-biodegradable, and improper disposal leads to landfill accumulation and environmental degradation. Governments are increasingly pushing for recycling initiatives, circular economy models, and reduced dependence on synthetic elastomers to minimize waste generation. This shift is prompting manufacturers to explore biodegradable rubber alternatives and eco-friendly additives, but the transition is complex and requires long-term R&D efforts.
Competition from Alternative Elastomers
The market faces intense competition from other high-performance elastomers, such as fluoroelastomers, thermoplastic elastomers (TPEs), and silicone rubber, which offer comparable properties, including chemical resistance, high-temperature tolerance, and mechanical durability. Many industries, including automotive, aerospace, and industrial manufacturing, are exploring alternative rubber formulations that provide greater flexibility, sustainability, and cost-effectiveness. For instance, silicone rubber is preferred in applications requiring high heat resistance, while TPEs are gaining popularity due to their lightweight nature and ease of processing.
Another major challenge is the technological advancements in polymer blending, where manufacturers develop hybrid elastomers that combine the best properties of multiple materials. These innovations are putting pressure on XNBR producers to differentiate their products through improved formulations, value-added services, and enhanced product customization. To stay competitive, companies must focus on R&D investments, collaboration with end-users, and diversification into specialized applications.
Supply Chain Disruptions and Logistics Issues
The global supply chain for XNBR production and distribution has been significantly impacted by factors such as trade restrictions, shipping delays, and shortages of key raw materials. The COVID-19 pandemic, geopolitical conflicts, and labor shortages have led to longer lead times, increased transportation costs, and reduced manufacturing capacity. These disruptions have particularly affected industries that rely on just-in-time (JIT) inventory systems, causing delays in product availability and higher costs for end-users.
Additionally, climate-related disruptions such as natural disasters, extreme weather conditions, and resource scarcity pose further risks to the stability of the supply chain. The increasing frequency of hurricanes, wildfires, and floods in major industrial regions has the potential to halt production facilities, disrupt transportation routes, and damage raw material stockpiles. To address these challenges, XNBR manufacturers are adopting regionalized supply networks, digital tracking systems, and risk mitigation strategies to improve resilience and adaptability in an uncertain market landscape.
Market Opportunities
Increasing Demand in Industrial Applications
The industrial sector is a significant driver of the XNBR market, as industries require high-performance elastomers for seals, gaskets, conveyor belts, and mechanical components. With ongoing advancements in manufacturing automation, robotics, and industrial machinery, the demand for durable and chemically resistant rubber materials is expected to rise. The printing industry, for instance, is increasingly adopting XNBR-based rollers and printing plates due to their ability to withstand mechanical stress and chemical exposure.
Furthermore, the engineering and construction sectors are integrating XNBR-based coatings and adhesives into infrastructure projects, improving the longevity of bridges, tunnels, and roadways. The rising investment in smart factories and Industry 4.0 solutions will further drive the need for high-quality industrial components, positioning XNBR as a preferred material for long-lasting and resilient applications.
Expansion of the Asia-Pacific Market
The Asia-Pacific region is emerging as a key growth hub for the XNBR market due to its rapid industrialization, expanding manufacturing sector, and increasing infrastructure development. Countries such as China, India, Japan, and South Korea are witnessing rising demand for automotive components, industrial rubber products, and consumer goods, leading to greater adoption of XNBR. The presence of large-scale rubber processing plants, competitive labor costs, and government incentives for industrial expansion further boosts market growth in the region.
Additionally, the growing middle-class population and rising disposable incomes are driving the demand for high-performance consumer goods, including footwear, gloves, and sporting equipment. The strong export-oriented manufacturing ecosystem in Asia-Pacific allows manufacturers to supply XNBR-based products to global markets, strengthening regional competitiveness.
Growing Adoption in the Medical and Healthcare Industry
The medical and healthcare sector is emerging as a key growth driver for the Carboxylated Nitrile Rubber (XNBR) Market, particularly in the production of medical gloves, catheters, and other protective equipment. With increasing concerns over hospital-acquired infections (HAIs) and the rising need for durable, chemical-resistant, and latex-free medical gloves, XNBR-based gloves are gaining widespread adoption. The COVID-19 pandemic further accelerated the demand for protective medical gear, pushing manufacturers to expand XNBR production capacity. Additionally, XNBR’s superior puncture resistance and enhanced tactile sensitivity make it a preferred material for surgical and examination gloves, ensuring higher safety standards in hospitals and clinical settings. As global healthcare infrastructure expands, particularly in emerging economies like India, Brazil, and Southeast Asia, the demand for XNBR-based medical products is expected to grow significantly. Companies investing in medical-grade XNBR formulations and certified production facilities stand to gain a strong competitive edge in this rapidly growing segment.
Green Manufacturing and Sustainable XNBR Solutions
With growing concerns over environmental sustainability, companies investing in eco-friendly elastomer solutions have a significant opportunity to differentiate themselves in the market. The development of bio-based XNBR and recyclable elastomers is gaining traction, as industries seek sustainable alternatives to traditional petroleum-based materials. Innovations in low-emission rubber processing technologies can help manufacturers meet regulatory requirements while maintaining cost-effectiveness. Companies that focus on sustainability-driven product development will gain a competitive advantage and attract environmentally conscious buyers.
Market Segmentation
By Acrylonitrile Content:
- 8-18% Acrylonitrile
- 18-22% Acrylonitrile
- 23-27% & above
By Application:
- Belts
- Printing Rolls
- Hoses, Rings & Seals
- Gaskets
- Shoe soles
By End-Use:
- Automotive & Transportation
- Oil & Gas
- Paper Printing
- General Manufacturing
- Consumer Goods & Appliances
By Region:
North America
- U.S.
- Canada
- Mexico
Europe
- Germany
- France
- U.K.
- Italy
- Spain
- Rest of Europe
Asia Pacific
- China
- Japan
- India
- South Korea
- Southeast Asia
- Rest of Asia Pacific
Latin America
- Brazil
- Argentina
- Rest of Latin America
Middle East & Africa
- GCC Countries
- South Africa
- Rest of Middle East and Africa
Regional Analysis
North America
North America remains a major hub for XNBR consumption, driven by automotive production, aerospace applications, and industrial machinery demand. The presence of leading rubber manufacturers and strong R&D investments supports product innovation and technological advancements. The United States and Canada are witnessing growing demand for XNBR-based components in oil & gas exploration, medical applications, and industrial gloves, further expanding market opportunities.
Europe
Europe’s market growth is fueled by stringent environmental regulations that push manufacturers to adopt sustainable and high-performance elastomers. Countries like Germany, France, and the UK are leading consumers of industrial-grade rubber materials. The rising demand for EV components, medical equipment, and consumer goods is further accelerating market expansion.
Asia-Pacific
Asia-Pacific is the fastest-growing region for the XNBR market, primarily due to China and India’s booming manufacturing and automotive industries. The expansion of industrial production, infrastructure projects, and increasing investments in oil & gas sectors make this region highly lucrative for XNBR manufacturers.
Latin America
Latin America is experiencing steady growth in XNBR demand, driven by automotive production, oil exploration, and the industrial manufacturing sector. Countries like Brazil, Mexico, and Argentina are leading the market expansion, supported by rising investments in heavy industries.
Middle East & Africa
The Middle East & Africa market is driven by the growing oil & gas sector, as XNBR is extensively used in seals, hoses, and drilling equipment. Countries like Saudi Arabia and the UAE are investing heavily in petrochemical infrastructure, creating sustained demand for high-performance elastomers.
Top Companies
- Zeon Chemicals
- LANXESS AG
- LG Chem
- JSR Corporation
- Synthomer PLC
- Nantex Industry Co., Ltd.
- Kumho Petrochemical
- Omnova Solutions Inc.
- Sibur Holding
- AirBoss of America Corporation
Future Outlook
- The increasing demand for XNBR in automotive, oil & gas, and manufacturing industries will drive steady market growth over the next decade. The material’s superior durability and chemical resistance make it indispensable in industrial applications.
- The rise of electric vehicles (EVs) is expected to boost the demand for XNBR-based components, particularly in battery seals, gaskets, and high-performance hoses, as manufacturers seek durable materials that withstand extreme conditions.
- The oil & gas industry’s expansion, especially in deepwater exploration and shale gas extraction, will further drive the need for XNBR in critical sealing applications, ensuring its continued market relevance.
- Advances in manufacturing technologies, including automation and precision engineering, will enhance production efficiency, lower costs, and improve product consistency, making XNBR more accessible to a broader range of industries.
- Sustainability concerns are prompting manufacturers to develop eco-friendly XNBR alternatives with lower environmental impact, aligning with global regulatory trends and consumer preferences for greener materials.
- The Asia-Pacific region is expected to dominate the market, driven by rapid industrialization, strong automotive manufacturing, and increasing investments in infrastructure, particularly in China, India, and Japan.
- Stricter environmental and safety regulations will push companies to innovate and adopt sustainable production methods, making compliance a key factor in gaining a competitive edge in the global market.
- Research and development investments will lead to enhanced XNBR formulations with improved wear resistance, elasticity, and chemical stability, expanding the material’s applications across various sectors.
- The consumer goods industry is witnessing growing demand for XNBR in applications such as footwear, protective gloves, and industrial equipment, contributing to steady market growth.
- Strategic partnerships, mergers, and acquisitions among key players will shape the competitive landscape, enabling companies to expand their market presence and leverage advanced technologies for long-term success.
Check out the full study: https://www.credenceresearch.com/report/carboxylated-nitrile-rubber-market